Water Underwater?
One of the significant factors in feed production is the ingredients’ moisture content. At various times, this needs to be raised or lowered to produce a particular consistency or otherwise alter a particular characteristic of the ingredients. This makes it vital to have an accurate measurement of the moisture content at each significant processing stage, as this figure will affect the operation of subsequent stages, have an impact on the quality of the final product, and determine how much energy is used and waste produced.
Fish feed comes in multiple forms and a wide variety of formulations, each with its own mix of ingredients.
For each of these different mixes, fish feed producers process the raw ingredients through several similar stages, including storage, milling, drying, conditioning, and pelletising.
Throughout these steps, fish feed manufacturers strive to improve the protein ratio of their products and improve their profitability while also saving energy, cutting waste and reducing their carbon footprint.
Storage
The ingredients must be stored and preserved correctly to prevent mycotoxins, spoilage, or heat spots. These problems are often directly related to the moisture content of the ingredients, so monitoring water content whilst transferring into storage is important in order to prevent them.
Drying
Drying is a common practice to ensure materials are stored safely, but reaching the perfect moisture content target is not easy. If not reached, the ingredients are prone to mycotoxins and spoilage – on the other hand, over-drying is not only an expensive waste of energy but can also cause damage, shrinkage, and loss of yield.
The material entering the drier has a continually varying water content, which makes it challenging to regulate the time the material needs to be exposed to heat or to regulate the temperature.
In this process, inline moisture control is used to automate the dryer to save energy costs and improve quality.
Conditioning
After drying, depending on the material and system requirements, it may be necessary to reintroduce moisture into the product by conditioning. This can be done before milling/grinding or pelleting operations.
Depending on the final application, the conditioning process can also involve heating the material to kill bacteria, to cook ingredients, and gelatinate starch.
In the same way that moisture control enhances the drying phase, it also improves the conditioning process by reacting quickly to changes in the moisture content of the input material.
Grinding
Grinding is one of the most energy-consuming transformations in many feed processes. Through mechanical action, it reduces the size of feed materials such as grain, seed, fruit, and many more to achieve different levels of chemical and microbiological stability.
The results of grinding processes can vary based on the machines and methods used, as well as the toughness and moisture content of the processed material.
Toughness is the ability of a material to resist breakage, meaning tougher material will need more mechanical energy to reduce its size.
The plasticity or ductility of a material determines the amount of energy absorbed before breaking down, as well as its final size. More plastic or ductile materials will need more energy to break them up, but they will also maintain a more regular final shape. In contrast, less plastic or ductile materials will shatter into finer and irregular shard-like particles.
The plasticity of the material is affected by its water content. This means that, by controlling the moisture of the material, it is possible to determine the energy consumption of the process, the final size of the powder particles, and the product yield and loss.
For these reasons, the initial moisture content of fish feed materials is the most important aspect to regulate before the grinding process starts.
Pelletising
Pelletising is the process of extruding the formulation into cylindric shapes that are more easily consumed by fish. The content of the mix is hugely variable between the various applications and formulations. However, even in this process, water content is still an essential factor in the quality of pellets.
Drying pellets
The final drying stage is essential to ensure pellets offer maximum shelf-life and quality.
As outlined earlier, drying is a delicate procedure where it is important to achieve a specific water content, and inline moisture control will help manufacturers to adjust to the variation in the material.
Control and sensors
As we have seen, the moisture content affects the costs and the quality of the products.
Knowing and thus controlling the water content of the material at every stage of the process is necessary to improve efficiency, reduce carbon footprint, and save money.
By controlling the moisture during the process, it is also possible to calculate the protein content of the pellet and guarantee superior product quality.
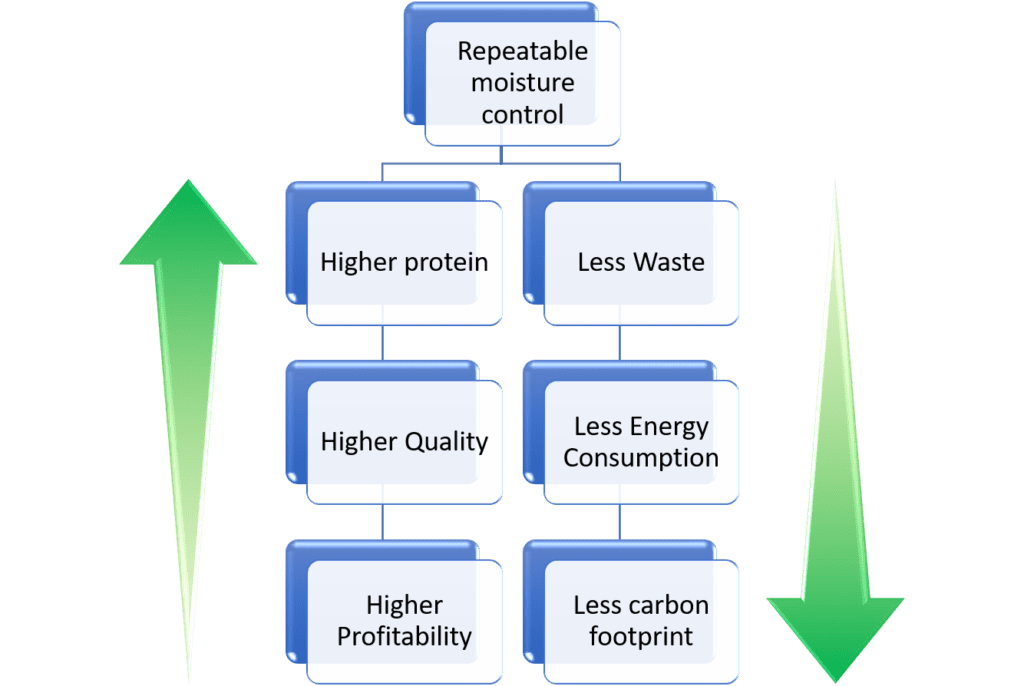
Periodic sampling of the material will not be enough to achieve these results because the samples may not be representative of the full batch – the speed of the feedback process is also not adequate to achieve the real-time control needed. This is only possible with inline sensors.
The solution is to use an online moisture sensor. This type of sensor is designed to give a fast response to water changes in the material to enable a control system to give precise control of the moisture.
All sensors measure the water content indirectly – so it is calculated from another measured property. To do this accurately, it is important to keep the material conditions as consistent as possible. Factors that can affect the measurement are:
- Material composition
- Particle size
- Pressure on the sensor
- Flow rate
- Sensor position
For this reason, it is vital to calibrate the moisture sensors for each material following final system installation. The calibration must be undertaken based on accurate lab tests, as simply calibrating a sensor with the readings of another different sensor can lead to a series of accumulating errors. The result is incorrect calibrations, defeating the objective entirely.
Independently from the measurement method used in the process, it is also vital to completely remove moisture from the sample to reach the dry weight during the lab test. This weight is what will be used while calibrating the sensor to define the moisture reported by the sensor.
Are all sensors equal?
There are many types of moisture sensors available on the market, based on different technologies. They can all be summarised in six categories:
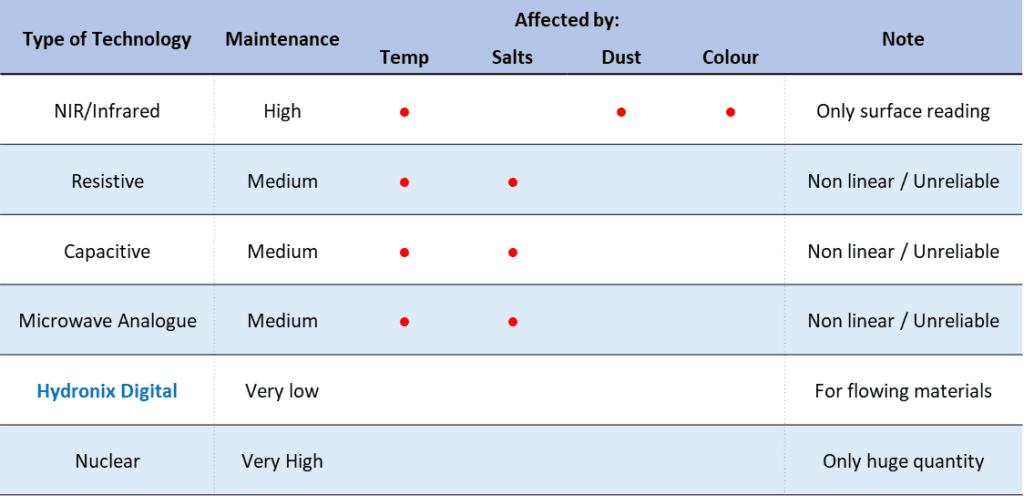
An essential but often overlooked difference in the digital microwave technology is the linearity and stability of the measurement. Resistive, capacitive, and analogue microwave sensors have a nonlinear measurement, making them very difficult to calibrate as they require numerous points to design the curve. Nonlinearity also implies low accuracy at the wet and dry ends of the scale.
By contrast, sensors with a digital measurement technique have a linear measurement, meaning that the sensor reading and water content are directly and proportionally related.
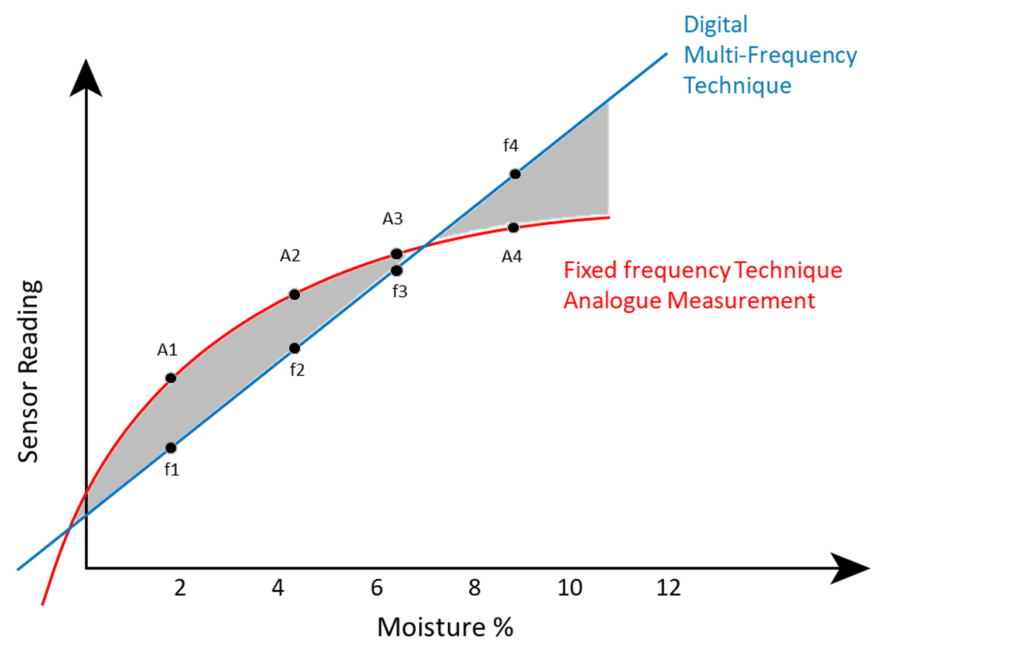
This method allows systems to achieve optimal calibration with a few points. Theoretically, it is possible to achieve calibration with only two points with a linear system.
By contrast, sensors with a digital measurement technique have a linear measurement, meaning that the sensor reading and water content are directly and proportionally related. This method allows systems to achieve optimal calibration with a few points. In theory, with a linear system, it is possible to achieve calibration with only two points.
Defining the ideal sensor
With these considerations in mind, it is possible to define the ideal requirements of a moisture sensor:
- Inline with multiple readings per second, providing quick feedback for the control to adjust every batch.
- Robust, made with high-quality materials to withstand tough industry conditions.
- Linear measurement, repeatable and stable over time, precise in every condition and simple to calibrate to enable an accurate output.
- Can store multiple calibrations to be used with different materials.
- Able to measure into the flow of the material.
- Unaffected by dust, colour, or variations in salt and mineral content.
- Self-contained and easy to integrate into existing systems.
- Low maintenance and cost-effective.
- Able to monitor and configure remotely for flexible connectivity and analysis.
All the above characteristics can be found in Hydronix microwave sensors, which incorporate a unique digital microwave technology built to resist the harshest conditions.
Hydronix is present in over 80 countries around the globe, with a network of expert engineers ready to provide service to companies wherever they need to measure moisture.