Concentration Measurement in Cocoa Powder Production
When manufacturing powders, for example, dried drinking chocolate, it is common practice to concentrate a liquid before spray drying and this is typically done in an evaporator. The material is then processed through the spray drier where the remaining moisture is evaporated leaving fine particles of powder. Measuring the precise level of concentration of the liquid can achieve considerable savings in the reduction of waste materials and also provides increased and consistent product quality.
The Process
Production of a powdered drink product consists of agitating the ingredients in a low-pressure 0.8 bar Evaporator at a temperature of between 50-60°C until the mixture has reduced to a pre-determined consistency. This process takes approximately 1½ hours and when the mix has reached the desired level it is then discharged from the vessel and transported to a spray drier. The drier evaporates the remaining excess moisture and the powder is then discharged into a crusher to prepare it for packaging. If the material is at an incorrect moisture level after the Evaporator, this can result in a low or variable quality product and in the worst case could become a fire hazard in the drier.
Known Problems
Inside the Evaporator there are agitators which rotate to keep the mixture moving in the vessel. As the product thickens, the power required to drive the agitators at the same rate increases until a set point is reached and the Evaporator is discharged.
It is possible to measure the current of the motor power supply to determine when the material is ready for discharge. However, if there are variations caused by the changing temperature of the material in the Evaporator, (which also affects product viscosity), or any changes in the temperature of the Evaporator gearbox oil, the final load on the power supply may fluctuate. The repeatability of this basic control method is very unreliable which in turn leads to variations in the quality and consistency of the material discharged from the Evaporator.
The Hydronix Solution
By using a Hydro-Probe BX digital microwave moisture sensor in the Evaporator it is possible to achieve a very accurate measurement of the material concentration.
The Hydro-Probe BX uses the unique Hydronix Digital Microwave Measurement technique and has been specifically designed to measure moisture content or Brix (sugar) in an evaporator or other pressurised environment where high temperatures may be used during processing. The sensor is capable of measuring the degree of dissolved solids in a liquid and may be calibrated to either moisture percentage or Brix.
Recommended Installation
Installation of the sensor is dependent on the application. Hydronix would recommend that the Hydro-Probe BX is installed at a small angle to the horizontal in the Evaporator for the best results.
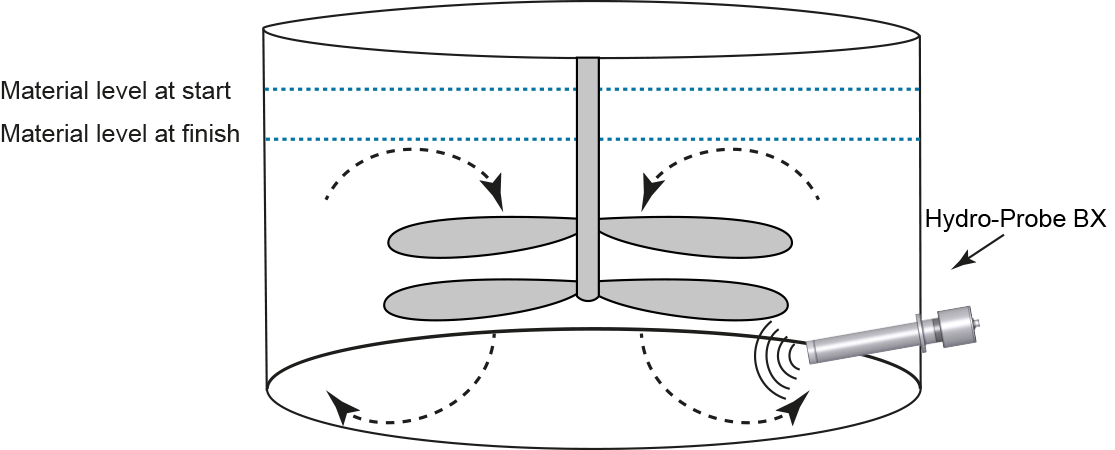
The graph in Figure 2 is a typical reading from an automation system. The output from the Hydronix Hydro-Probe BX is shown in blue and the red line is the measurement of the motor input current. It can be seen that the final current varies significantly from batch to batch regardless of any longer-term variance. The reading from the Hydro-Probe BX has a linear change with time which can be used to precisely target a repeatable material concentration.
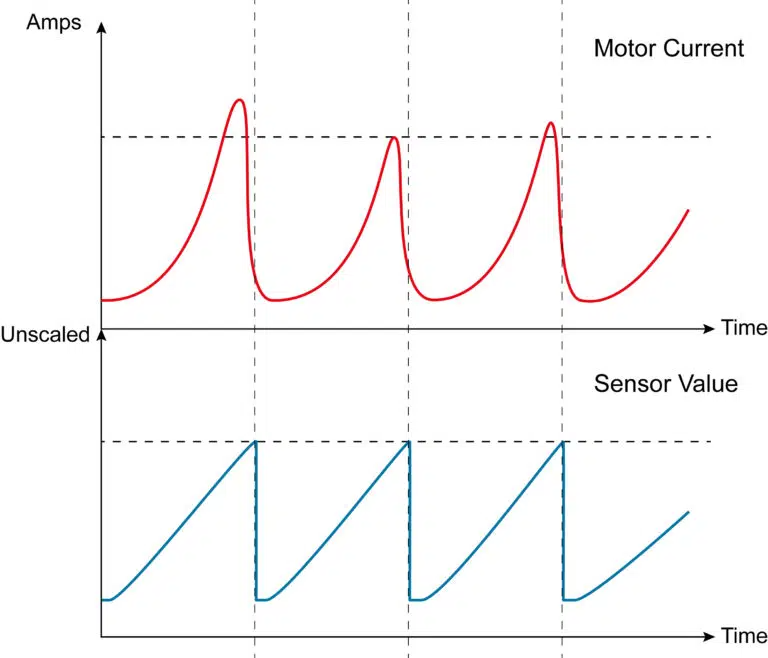
The Hydro-Probe BX Sensor
The Hydro-Probe BX builds on the success of the Hydronix digital microwave sensors to allow measurement of Brix or moisture in a body that is designed to withstand high temperature and pressure processes. The sensor incorporates a number of signal filters and onboard functionality making the sensor very flexible and simple to install and commission. It is also capable of separately measuring the material temperature. These measurements can be output on two analogue control loops for integration into standard control systems.
The sensor can be configured using the Hydro-Com sensor configuration and calibration software and maybe either calibrated to output an absolute moisture or Brix value or alternatively to output the Hydronix factory calibrated value known as the Unscaled value. This is a range of values between 0 and 100 and can be used to determine and control
to a set-point to give an extremely precise and repeatable result without needing the extra laboratory calibration, when repeatability is the main requirement.
A significant advantage of using sensors with a factory-calibrated variable is that, in the event of replacing a sensor or temporarily removing a sensor for maintenance, a replacement unit may be installed and the calibration data of the previous sensor loaded in the new sensor.
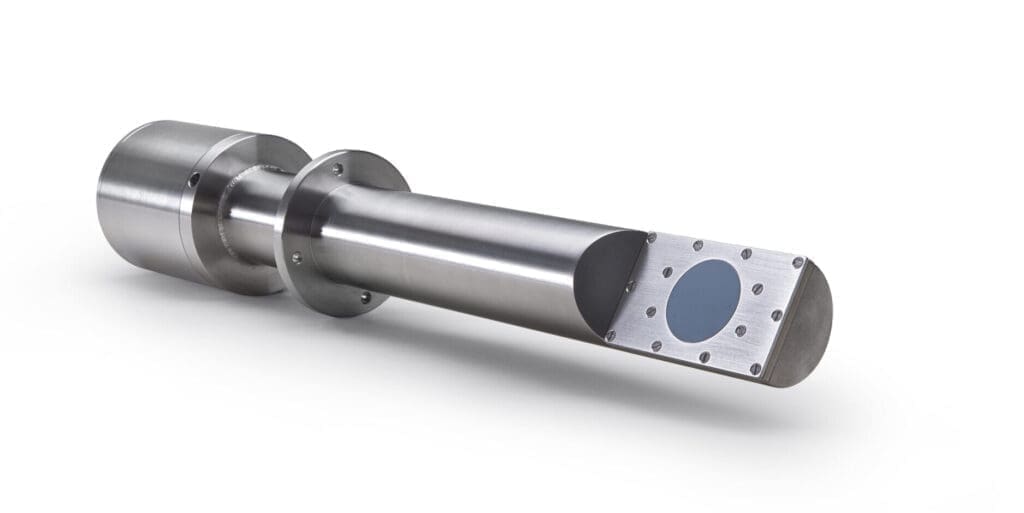
Result after Installing the Sensor
A correctly installed and commissioned system will measure the moisture levels of the materials in the vessel to an accuracy of +/- 0.2% providing a more accurate method of determining when the correct product consistency has been reached and the material is ready to be discharged.
Real-time control ensures that the material can be discharged at the exact point of consistency resulting in increased energy efficiency and a reduction in the amount of substandard or wasted product, as the process output will always be consistent batch after batch.